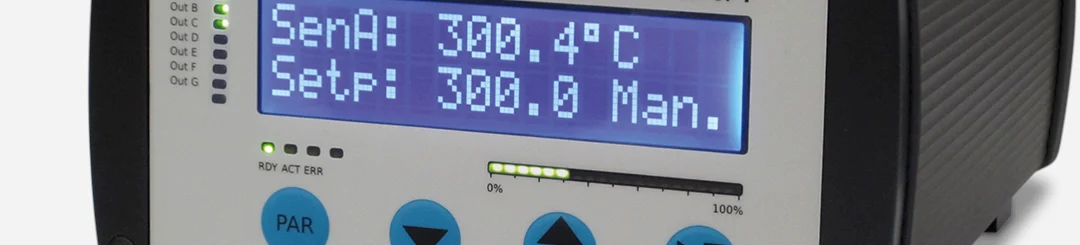
System Components
System components are additional components for special measuring tasks. They are used to expand the application possibilities of pyrometers. Contact us if you need assistance in your application.
Digital display IF0000 for temperature display, pyrometer setting and with switching outputs
For connecting a Sensortherm pyrometer via the interface and
- to display the measuring temperature
- for displaying and adjusting pyrometer parameters
- for activating switching outputs at temperature events
Details IF0000
- Easy to read 4 digit, 7 segment LED display
- Automatic detection of Sensortherm pyrometers
- Access and settings of all pyrometer parameters without PC
- Additional parametrizing of the pyrometer utilizing SensorTools software
- 4 switching outputs
- Interface output RS232 / 485 (switchable)
- Temperature display and evaluation via standard software SensorTools
PID controller REGULUS RF / RD with programming function
REGULUS program controllers are very fast PID temperature controllers. Programmable and optimized for pyrometers, they can perform complex control sequences of heating processes. They generate a direct manipulated variable from the measuring signal of the pyrometer.
Datasheet REGULUS RF (for panel mounting) and RD (in desktop housing)
Details REGULUS RF / RD
Typical application is the process control of nearly all heating processes
- Inductive soldering
- Laser soldering
- Soldering under inert gas
- Specific preheating and reheating of welding processes
Functions
- Adaptable to nearly every induction system (also for modernizing existing systems with manipulated variable input)
- Direct output of a continuously adapted 0-10 V manipulated variable for controlling the high-frequency generator or the power component
- Auto-Tune function for automatic P-I control parameter determination
- Additional connection of up to 2 thermocouples possible
Timed heating ramps, holding times and cooling rates are selectively programmable. Intelligent APA (Automatic Process Adaptation) functions improve process control for soldering applications. The extensive logging functions of the SensorTools software are ideal for “online” monitoring and for subsequent analysis of the processes. The controller is able to take full advantage in the high requirements of the laser power control. Applications such as laser hardening, laser soldering or laser welding are no problem due to an extremely fast sampling time of only 100 μs.
- Extremely fast sampling time of 100 µs
- 990 program steps can be divided into 26 programs
- Automatic detection of Sensortherm pyrometers
- Measurement range overlap control
- AutoTune function (automatic P-I determination)
- 7 digital outputs
- 6 digital inputs
- Emissivity adjustable for every program step
- Easy programming via software
- Also for modernization of existing plants with control input
Additionally at desktop housing model RD
- Two pyrometers can be connected (e.g. to enlarge the overall temperature range)
- Up to two thermocouple inputs possible, type S or K
- 4 limit relays: 230 V, 6 A
SensorTools is the standard software that is used to program the REGULUS, after which the controller processes the programmed control steps completely independently. Operation with a PC connection also enables direct visual control of a running process.
- Controller configuration
- Creating and saving programs
- Recording and storing of controlling and temperature processes for documentation purposes
- Presentation and interpretation of stored events
- AutoTune function for automatic detection of useful P and I values
GALAXY SC7x / SC8x Temperature Scanner for up to 16 Measurement Regions
GALAXY line scanners move the spot size of a pyrometer continuously over objects and record temperatures at regular angular distancees. With an adjustable measuring angle between 0.56 and 90°, 10 to 1600 measured values can be recorded and evaluated.
Each of the up to 16 measurement regions can be evaluated separately. As soon as a region has been passed, the maximum, minimum or average temperature is provided at the analog outputs or even all of them are displayed together on the PC.
Details GALAXY
This enables extensive evaluations:
- Temperature profiles provide information about the temperature distribution between edge and middle object areas
- Maximum, average and minimum value of each scan of the material to be measured, provide a quick overview of compliance with the necessary object temperatures
After the measurement regions have been set up, the GALAXY
- can be operated independently without a PC via separate analog outputs for each measurement region
- can be operated with a PC for graphical display and evaluation of the measurement results, e.g. to generate surface images as with thermographic cameras
Installed in a cooling housing, the GALAXY can also be used under harsh conditions.
SC10 scanners continuously move the measuring field of a pyrometer back and forth. They are mainly used to detect the maximum temperature of objects, where at fixed aligned pyrometers the measuring object would move out of the focus (e.g. thin wires) or cold parts of surfaces (e.g. scale) would not display the correct temperature.
Details SC10
Field of Application
- Peak value temperature measurement of smaller measuring objects
- Measurement of thin wires
- Detecting scale-free points on scaled metal surfaces
- Detection and measurement of hot spots
- Temperature peak detection of slabs, billets or steel strips
The heavy-duty measuring system is is designed for the harsh environments in the steel industry. The optics are rated up to 250°C and the purge air provides additional cooling which keeps the optics and field of view free of contaminants. The electronics module can be mounted up to 30 meters away in a protected position.
Datasheet Heavy-duty measuring system
Steel industry temperature monitoring
Details HD Measuring System
Designed for continuous temperature measurement in:
- Hot strip rolling mills
- Continuous casting plants
- Casting machines / automatic casting units
- Pipe welding machines
- similarly harsh industrial conditions
Precise measurements under hardest conditions:
- Can be combined with METIS 2-color or 1-color pyrometers
- With METIS high-speed models for measurements at high belt speeds
- Use up to 250°C on the measuring head without additional cooling
- Air purge for the optics system
- Extremely resistant stainless steel braided hose
The system is optimally adapted to the application conditions in the steel industry. The optics system is designed for up to 250°C, the purge air provides additional cooling and keeps the optics tube and thus the pyrometer field of vision free from contamination. The electronics of the measuring system is mounted in up to 30 meters in a protected position.
- Flexible application by remotely adjustable emissivity and innovative automatic process adaptation
- Special pouring stream mode available as an option
- Customer-specific recalibration possible
- Highly accurate measurements by latest processor technology and fully digital signal processing
- Fastest exposure times
- Smallest spot sizes
- sing the peak picker allows to detect even smallest scale cracks which represent the “real” temperature to be measured
Application example hot strip rolling mill
In this application it is measured by the pyrometer from below of the strip, so that the measurement result is not affected by scale or water puddles on the strip. The evaluation unit is remotely installed in the control cabinet. The measuring tube is kept free from contaminants with flush air.
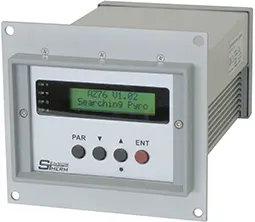
Measurement Data and Maximum Value Storage AZ76
The AZ76 uses the temperature measured with a pyrometer to determine the maximum temperature of passing objects. The AZ76 compares these values with a specified temperature range in order to provide a corresponding control signal if they match or deviate (via 4 switching outputs for the states overheated, too warm, good or too low).
Details AZ76
Each measured value with valuation result, date and time is stored in the device (max. 32000 records). Data can be read out via interface commands or via the external software SchmiedeWin. SchmiedeWin können die Daten ausgelesen werden.
4 signal inputs can be used to transmit switching signals to the AZ76 of successfully changed switching gates to the correct position, and save in the log.
A common use of AZ67 is for the quality assurance and logging in forging that measure a forging blank and control a switch for the reject for non-compliance with the temperature required:
Too hot –> Reject
Too warm –> Reenters the circulation (parameter is optional available)
Good –> Production
Too low –> Can be re-heated and enters the circulation