
Applications
The use of pyrometers is always required when processes are to be monitored and optimized. Continuous temperature monitoring with pyrometers enables temperature deviations to be detected in order to produce a high-quality end product.
The material to be measured determines the pyrometer's spectral range, the listed areas of application lead to a pyrometer recommendation. If necessary, let us advise you on your application or on complicated measuring tasks.

Pyrometers for Laser Process Control and Temperature Control
Highspeed pyrometers with an integrated controller measure the temperature and thus control a given temperature level at the same time. The controlled laser power ensures a consistent quality of the processed material, even where changes of laser beam delivery would cause discontinuities in temperatures.
Application datasheet laser power control
Application datasheet for temperature-controlled process control
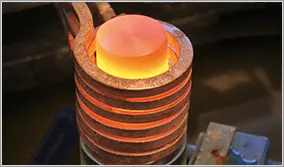
Inductive Heating
A pyrometer in combination with a PID program controller REGULUS provides the fastest and most efficient method to rapidly detect temperature variations on inductively heated components and directly provides a 0-10 V manipulated variable for controlling the high-frequency generator.
Application datasheet for pyrometer workpiece monitoring with simultaneous temperature control
Learn more
Induction heating has established itself as a fast and efficient method for heating metallic or electrically conductive materials in industrial production. Modern induction systems quickly generate targeted workpiece temperature necessary for the process.
The necessary process temperature must be achieved as precisely and evenly as possible and hold for the required time to prevent material structures from being changed or even destroyed.
The best solution for this is the fast non-contact temperature measurement with pyrometers as well as the control with specially developed temperature controllers.
With a combination of pyrometer and program temperature controller:
- Temperature changes on the inductively heated component can be detected very quickly and
- A continuously adjusted control variable for controlling the high-frequency generator is provided to the output
Functions of the programmable temperature controller REGULUS:
- Manual mode for easy ramps and hold times
- Program mode for direct approach to various setpoints, including ramp or time control
- Automatically determine useful control parameters
- Visually track, store, evaluate and document all processes via software
- Ability to make many more adjustments for every conceivable heating task
Our pyrometer recommendation:
SIRIUS SI23 is a 1-color pyrometer with temperature ranges from 50°C, 5 ms response time and spot sizes from 1.3 mm, laser targeting light as an alignment aid and a fixed focus optics with adjustable lens position to adjust the focus distance.
METIS M323, M318, M316 or M309 are 1-color pyrometers with temperature ranges from 50, 100, 200 or 550°C, 1 ms response time, very small spot sizes from 0.4 mm, with a focusable optics and laser targeting light, throug-lens view finder or camera module as an alignment aid.
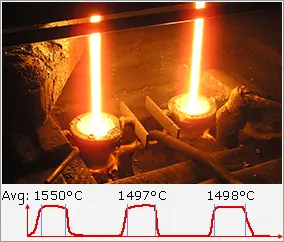
Pouring Stream Monitoring
Intelligent pyrometers with pouring stream mode automatically detect the entire casting process and provide an average temperature of the complete cast. Disturbances such as hot slag spillings or drop at the beginning or end of the casting are automatically detected and eliminated from the final temperature. Thus, the cast monitoring ensures a consistent quality assessment of the end product.
Datasheet METIS M311 pouring stream: 2-color pyrometers with pouring stream mode are non-sensitive to dust and smoke and easy to align.

Rolling Mills, Continuous Casting Plants,…
The heavy-duty measuring systems in heavy stainless steel construction is designed for continuous temperature measurements in rolling mills, continuous casting plants and similarly harsh industrial conditions.
GALAXYline scanners in continuous casting plants and rolling mills are used to monitor the temperature of several continuous casting profiles or above the laying machine in the wire rod rolling mill.
Application datasheet steel industry temperature monitoring with well protected flexible pyrometer measuring systems.
Learn more
The optics system is designed for ambient temperatures up to 250°C, the purge air provides additional cooling and keeps the optics tube and thus the pyrometer’s sighting field free from contamination.
The electronics of the measuring system is mounted in up to 30 meters in a protected position.
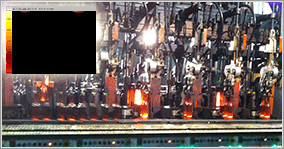
Glass Gob Measurement
Short-wave 2-color pyrometers are capable of detecting the glass temperature slightly below the surface. Thus, the measurement is not affected by a possibly cooled surface and is easy to evaluate. The measurement of the temperature distribution of glass gobs allows the optimization of heating processes.
Datasheet METIS M311 / M322: 2-color pyrometers
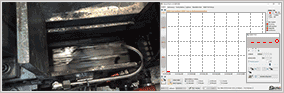
Temperature Profile Measurement
Highspeed pyrometers are able to create a detailed temperature profile from quickly passing parts. Using slower devices, detailed information is smoothed and does not allow an evaluation of important information. For example, it is thus possible to draw conclusions about different material thicknesses.
Datasheet METIS H309 / H316 / H318: High-speed pyrometers
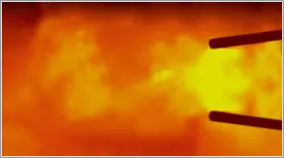
Flame Measurements
Special flame pyrometers for non-contact temperature measurement of sooty flames in coal-fired power plants, waste incineration plants and other incinerators are used to optimize combustion operation and to reduce emissions in combustion chambers or to avoid slagging of combustion chamber walls.
Datasheet METIS M3F1: 2-color pyrometers for temperature measurement of sooting flames
Wire Measurement
2-color pyrometers with a line optics have an elongated measuring field that is particularly easy to measure thin wires or small objects that move and would run out of the measuring field with round standard measuring fields.
Datasheet METIS M311 / 22 with line optics: 2-color pyrometers for measuring moving objects
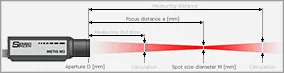
Spot Size Calculator
The spot size calculator is used to calculate the spot size diameter in front of and behind the focused measuring distance. To do this, the basic data must first be entered (see spot size table in the respective pyrometer operating manual), then the spot size can be calculated at a desired measuring distance.